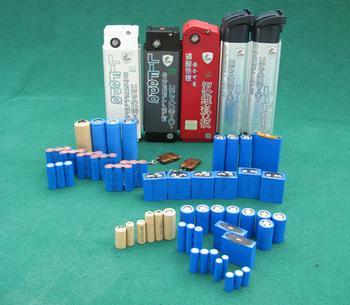
First of all, the recycling of materials needs to meet the following conditions: to reduce environmental pollution, energy conservation, to address the supply gap, in line with laws and regulations, have the raw material supply conditions, with scale effect, the most critical is to have economic benefits. At present, in the recycling and recycling of lithium batteries, high-value cobalt, nickel, copper and other materials are mainly extracted, and the cost of regenerating lithium carbonate is estimated to be more than 40,000 yuan/ton (according to foreign media reports, from lithium batteries The cost of recovering lithium carbonate is five times the minimum production cost of lithium carbonate. If the cost of SQM with the lowest cost of lithium carbonate production is calculated, the cost will be more than 40,000 yuan/ton, which is much higher than the cost of primary lithium carbonate. Unprofitable, so recycling companies have almost given up recycling of lithium.
1. The pyrometallurgical method only recovers high-value materials
At present, lithium batteries are mainly used in consumer electronic products, so the recovered lithium batteries are all small batteries. Lithium batteries and nickel-metal hydride batteries generally contain high-value materials such as cobalt and nickel. Recycling companies generally adopt technology-based dry metallurgy to recycle elements such as cobalt, nickel, and copper, and elements such as aluminum, lithium, and manganese. Less recycling. Advantages of the dry process: The combustion of organics in batteries provides energy; cobalt, nickel, and copper are recycled (cobalt recovery saves energy costs by 70%; there is no emission of sulfur-containing gases). Lithium and other residues can be added to the concrete after recycling to improve performance. Umicore, Belgium's leading global battery recycling technology, uses dry metallurgy to recover elements such as cobalt, nickel, and rare earth elements, and it has not recycled lithium and manganese elements due to non-economic benefits.
2. Lithium-powered battery recycling: low lithium recycling benefits
Lithium-powered batteries are important components of new energy vehicles. The disposal of used batteries involves safety and environmental protection. The recycling of batteries is an important part of the development of new energy vehicles. At present, most countries have not yet established the recycling of lithium-ion batteries for new energy vehicles. system.
Lithium-powered battery recycling and recycling will have two forms: one is to continue to apply in the lower-required areas after recycling, such as Nissan will use lithium batteries for secondary use in the field of backup power; one is to directly recycle recycling recycling useful material.
Lithium-ion battery after a single application is completed, all kinds of performance will appear a certain decline, so in the secondary applications, mainly used in areas with lower performance requirements, mainly in the residents of the backup power supply, energy storage equipment in remote areas. In the field of large-scale wind power generation and photovoltaic energy storage equipment, due to high requirements, the probability of secondary use of lithium-powered batteries is low. The field of secondary use is relatively new to the current consumer sector and has no impact on our supply and demand forecasts. The use of lithium battery recycling scrap recycling has a certain impact on the supply of lithium carbonate, so we mainly discuss the impact of this situation on the supply side.
3. Hydrometallurgy mainly recycles high-value materials
At present, the commercial method for lithium battery recovery to extract lithium carbonate is hydrometallurgy. Hydrometallurgy classifies waste battery raw material requirements and processes it at low temperature, but extraction of lithium carbonate is basically unprofitable. Still come from cobalt, nickel, copper earnings. The world’s leading lithium battery recycling company, Toxco, uses this method to recover, 60% of raw materials are recycled, and 10% of raw materials are recycled. Rookwood set up an experimental factory in support of the German Ministry of Environmental Protection in 2009. It hopes to use the hydrometallurgy technology to recover lithium from lithium-powered batteries more economically. There is no breakthrough at present.
At present, nickel-metal hydride batteries contain elements such as nickel and rare earths, and lithium-battery-based cathode materials containing cobalt and nickel elements, recycling companies using dry metallurgy and hydrometallurgy are still motivated to recover cobalt, nickel, etc. from batteries. Thin expensive elements. However, if lithium batteries are used in the future without positive or negative cobalt and nickel cathode materials, the use of dry and wet methods to recover lithium batteries will be unprofitable, and lithium carbonate will not be considered for recycling.
4, the physical method is the best, but the consistency of used batteries is difficult to meet
If cobalt, nickel and other rare-earth materials are used, the value of raw materials may be very low, but the value of cathode materials may be high. Therefore, the goal of recycling will no longer be raw materials, but direct recycling will have higher value. Cathode materials, anode materials, electrolytes, separators and other intermediate products.
At present, advanced battery recycling technology that has not yet been commercialized is a physical method. This method can directly recover positive electrode materials, negative electrode materials, electrolytes, and separators, and can be used again in lithium batteries after relatively simple treatment. This method is handled in a low-temperature environment, but the requirements for lithium batteries are extremely strict: they need to be the same kind of lithium battery (at least the positive and negative materials and electrolyte used in lithium batteries). The American company OnTo is currently studying this method and has a number of patents.
At present, there are many types of lithium battery cathode materials, and the proportion of nickel-cobalt-aluminum ternary materials is also inconsistent. Therefore, in addition to technical difficulties, the consistency standard of lithium batteries is difficult to meet and commercialization is difficult. In the future, if standardization, chemical composition standardization, detailed battery labeling, and easy-to-disassemble assembly design are performed on lithium-powered batteries, physical methods may be commercialized.
If the physical method is commercialized after the conditions are mature, it will have a greater impact on the raw material supply end of the lithium battery. A large proportion of the newly added lithium-ion battery raw materials will come from the recycling of lithium-powered car batteries, including the recycling of lithium salts. However, the standardization of lithium-powered batteries has certain difficulties, especially the standardization of chemical composition. Even if it can be standardized, the scrapping of large-scale lithium-powered batteries will be at least after 2020, with little impact on the current supply of various raw materials.
The mining intrinsically safe Explosion Proof Vfd is used for frequency conversion of belt conveyor, scraper conveyor, fan, water pump, pump station and other equipment. This explosion proof motor starter has a variety of control modes to choose from, wide speed range, flexible speed control, strong anti-interference ability and long service life, which is the best choice for downhole frequency conversion speed control device.
Abb Vfd,Ac Variable Frequency Drive,Vfd Motor Drive,Flameproof Vfd,Explosion Proof Vfd,Explosion Proof Manual Motor Starter
FGI SCIENCE AND TECHNOLOGY CO., LTD , https://www.fgi-tech.com